An industrial robot often takes the shape of a jointed structure that may be configured in various ways. The most popular categories in the robot industry are Articulated, SCARA, Cartesian, Parallel (or Delta), and Cylindrical. Read More…
A recognized leader in automated assembly products. Stay competitive with Dixon's robotic screwdrivers, auto-fed screw & nut drivers, auto-fed part placers, parts feeding systems & assembly cells, including robotic assembly & vision. Every Dixon product is manufactured to assure accuracy & dependability for repetitive assembly. Dixon supports Machine Integrators with assembly products & stations. ...
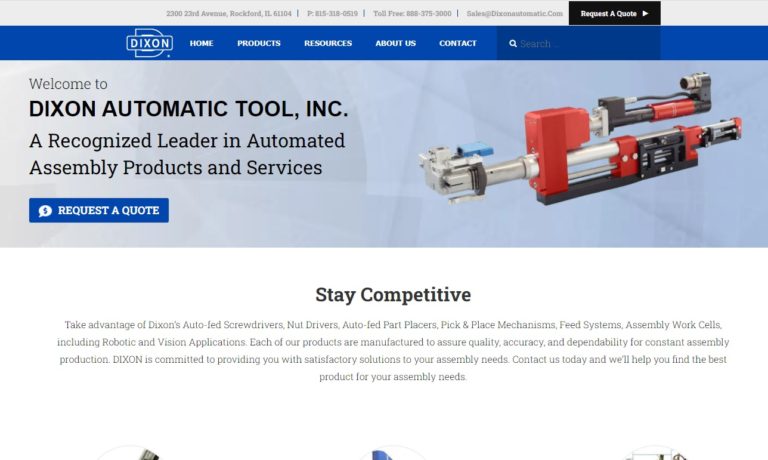
Invio Automation is a leading comprehensive AGV, AMR, and robotics integrator with 10 engineering and support sites throughout North America. We specialize in heavyweight and assembly line applications.
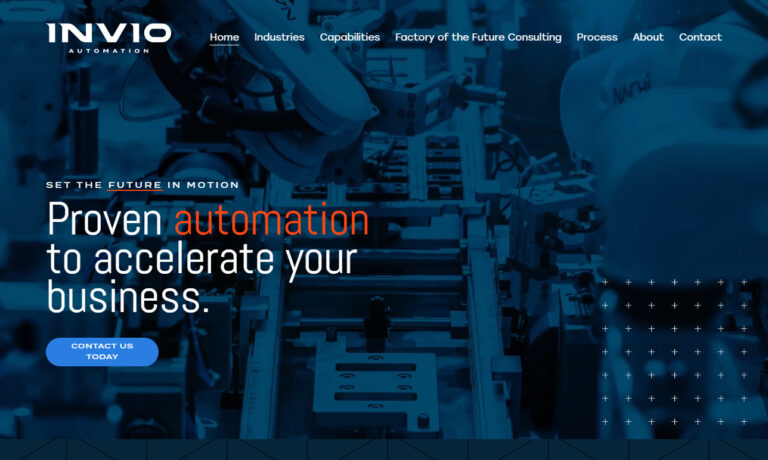
Advent design has been in business for over 35 years providing custom automation solutions, engineering, integration solutions and machine safety services. Contact us today to discuss your project needs and see how we can help you achieve your goals.
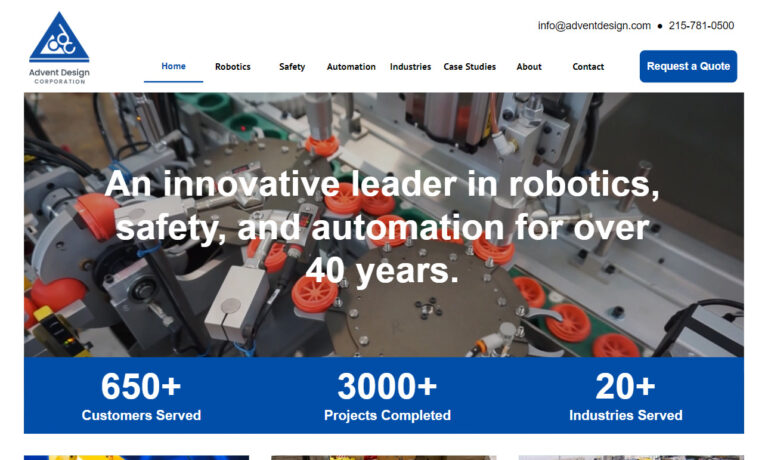
Since 1982, Isotech has been a leader in the automation equipment industry. You can trust the accuracy of our solutions. Our experts at Isotech are always available to assist you with your needs. Feel free to contact us today to learn more information!
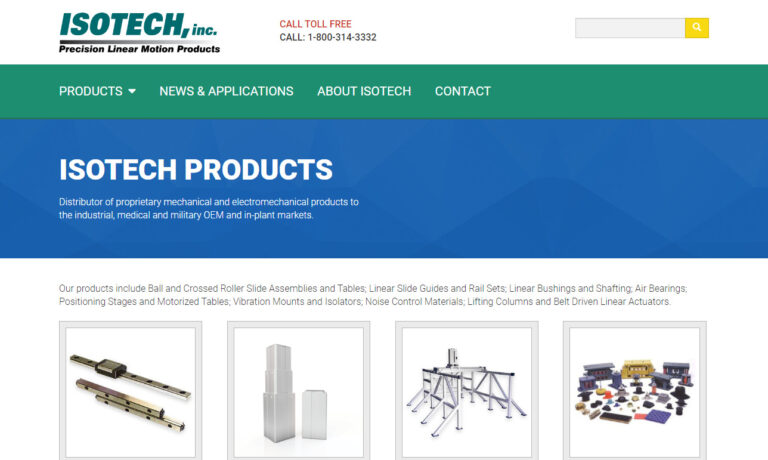
We have an extensive selection of products to pick from and we are confident we can find the perfect solution for your application. Our world-class items are proven for reliability and longevity. You can count on us to supply you with the best.
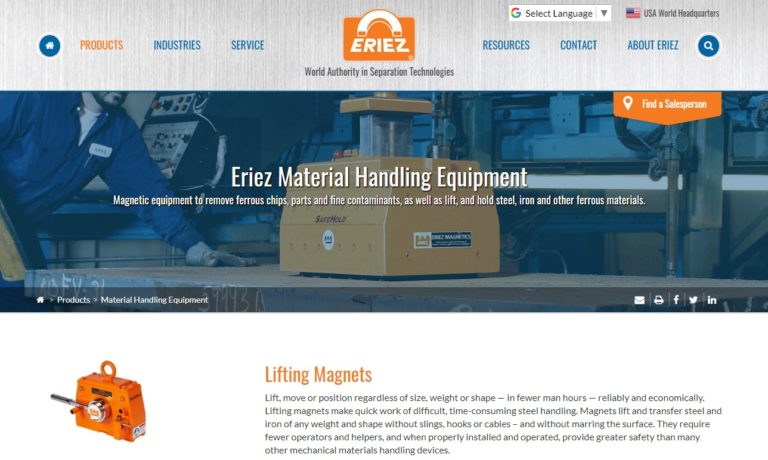
Del-Tron Precision is your one-stop shop for ball & crossed roller slides, multi-axis positioning and motor-ready lead screw stages, air actuators, recirculating slide guides and crossed roller rail sets. Custom linear slides are available.
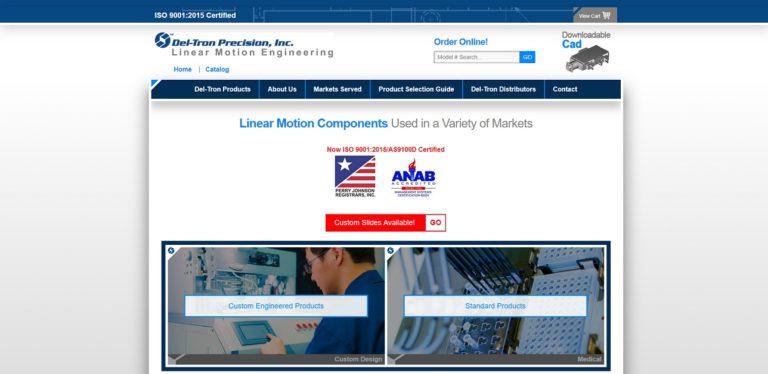
More Industrial Robot Manufacturers
Industrial robot architectures are created by connecting a variety of rotary and linear motions or joints. Each joint offers movement that, when combined, can place the robot framework, or robot arm, in a particular position. Six joints, or six degrees of freedom (more generally referred to as six axes), are needed to enable the capacity to position a tool installed on the robot's end at any location and any angle.
The area in which the robot operates is known as its working envelope. The robot may thus position a tool at any angle anywhere inside its active region. When a manipulator stretches out in all directions—forward, backward, up, and down—it forms this shape. The arm length and axis configuration of a robot affect these distances.
Articulated Robot
Articulated robots are those that have joints that can rotate. In robotics, these joints are frequently referred to as axes. Articulated robots, which often use servo motors to provide redundancy and improve access to tight locations, can be as simple as a two-axis construction or as complex as those with ten or more axes.
The jointed or articulated arm is the most typical configuration. This is incredibly flexible and closely resembles the human arm. Six rotational joints make up the framework, each mounted on the one before. They can position a tool in any orientation at a specified location and reach a point several ways within the operating envelope. Robots with articulated arms have complicated joint movements that can be challenging to visualize.
Each joint must support the weight of all the joints behind it; for example, joint three supports joints 4, 5, and 6 because of how the arm is built. These affect the robot's carrying capacity, the amount of weight it can lift, and its repeatability and precision. Structures are not particularly rigid, and the sum of all the axes determines the overall repeatability. However, most applications can now benefit from outstanding performance because of the rising performance of AC servo motors and advancements in mechanics.
Articulated robots use numerous processes, such as welding and painting. Typical robot sizes range from 1.6 to over 11.5 feet (0.5 to 3.5 m) in reach and from 6.6 to over 2204 pounds (3 to 1000 kg) in carrying capacity. In addition, some four-axis articulated arms have been created especially for tasks like picking, packaging, and palletizing, where the tool does not need to be oriented. As a result, only one wrist axe is needed instead of two. This robot can move heavier weights at faster speeds than identical machines with six axes.

SCARA
The articulated arm receives many benefits from the SCARA arrangement. The Selective Compliance Assembly Robot Arm arrangement was initially created for assembly purposes. The four-axis arm consists of a base rotation, a vertical linear motion, and two rotary motions occurring in the same vertical plane. The arm is extremely rigid in the vertical direction due to the arrangement and can also give compliance in the horizontal plane. It operates with extremely tight tolerances and offers fast speed and great acceleration.

Parallel or Delta
One of the most recent configuration advancements is the parallel or delta robot configuration. This comprises devices with concurrent prismatic or rotational joints on the arms. These were designed as above-mounted devices, with connected arms below driven by base structure-mounted motors. This method has the advantage of reducing arm weight, allowing extremely fast acceleration and speed capabilities. However, they can only carry a payload of less than 17.6 lbs (8 kgs).

Cartesian
All industrial robots that only have linear drives for their three main axes and whose motions follow a Cartesian coordinate system fall under the Cartesian category. Although certain specialized variants have been produced with additional rotating axes attached to the last linear axis, these devices are typically only capable of having three axes. Both linear pick-and-place tools and gantry machines fall within this Cartesian category. These have a variety of configurations and can also be built from modular kits, giving designers the freedom to create a machine that meets a particular need.
Goalpost-style gantries and area gantries with two support structures are two different types. Less than one meter to several tens of meters in length can be found for the primary axis. Gantries are capable of supporting 6614 lbs (3000 kg) and can be highly robust. The fact that gantries are primarily overhead means that they have little effect on the manufacturing floor and manual access to the equipment. However, they are frequently more expensive than robots with comparable articulated arms.

Cylindrical
The rotary and linear axes on these robots are often arranged in a pattern where the base rotates first. Next, there are vertical and horizontal linear axes, and finally, there are additional rotary axes at the wrist. They offer sturdy construction, good access to cavities, are simple to program and are straightforward to see. However, they need a room at the back of the arm. They are especially well suited for general pick-and-place tasks and machine tending.

Choosing the Correct Industrial Robots Manufacturer
To make sure you have the most productive outcome when purchasing Industrial Robots from an Industrial Robots Manufacturer, it is important to compare at least 4 or 5 Companies using our list of Industrial Robots suppliers. Each Industrial Robots Company has a business profile page that highlights their areas of experience and capabilities and a contact form to directly communicate with the manufacturer for more information or request a quote. Review each Industrial Robots business website using our proprietary website previewer to get an idea of what each company specializes in, and then use our simple RFQ form to contact multiple Industrial Robots companies with the same quote.